New Ways to Wire and Integrate Chips
New Ways to Wire and Integrate Chips MASTER CLASS May 26, 2022 Applied Materials External 1
Forward-Looking Statements and Other Information Today’s presentations contain forward-looking statements, including those regarding anticipated growth and trends in our businesses and markets, industry outlooks and demand drivers, technology transitions, our business and financial performance and market share positions, our investment and growth strategies, our development of new products and technologies, forecasts relating to our revenues, market share and other financial and business performance, and other statements that are not historical facts. These statements and their underlying assumptions are subject to risks and uncertainties and are not guarantees of future performance. Factors that could cause actual results to differ materially from those expressed or implied by such statements include, without limitation: the level of demand for our products, our ability to meet customer demand, and our suppliers' ability to meet our demand requirements; transportation interruptions and logistics constraints; global economic, political and industry conditions, including rising inflation and interest rates; the effects of regional or global health epidemics, including the severity and duration of the ongoing COVID-19 pandemic and government imposed lockdowns and other measures taken in response; global trade issues and changes in trade and export license policies; consumer demand for electronic products; the demand for semiconductors; customers’technology and capacity requirements; the introduction of new and innovative technologies, and the timing of technology transitions; our ability to develop, deliver and support new products and technologies; the concentrated nature of our customer base; acquisitions, investments and divestitures; changes in income tax laws; our ability to expand our current markets, increase market share and develop new markets; market acceptance of existing and newly developed products; our ability to obtain and protect intellectual property rights in key technologies; our ability to achieve the objectives of operational and strategic initiatives, align our resources and cost structure with business conditions, and attract, motivate and retain key employees; the variability of operating expenses and results among products and segments, and our ability to accurately forecast future results, market conditions, customer requirements and business needs; our ability to ensure compliance with applicable law, rules and regulations; and other risks and uncertainties described in our SEC filings, including our recent Forms 10-Q and 8-K. All forward-looking statements are based on management’s current estimates, projections and assumptions, and we assume no obligation to update them. Applied Materials, the Applied Materials Logo, and other trademarks so designated as product names are trademarks of Applied Materials, Inc. Other names and brands are the property of third parties.
2022 MASTER CLASSES WELCOME Michael Sullivan Corporate Vice President Head of Investor Relations NEW WAYS TO WIRE AND INTEGRATE CHIPS MASTER CLASS | MAY 26, 2022
2022 Master Classes APRIL MAY 21 26 New Ways New Ways to to Shrink Wire and Integrate Chips
9:00 PART 1 Mike Sullivan NDA Introduction and Fireside Chat with Regina Freed E Kevin Moraes, Ph.D. G Solving the Resistance Challenges of EUV Scaling A Mehul Naik, Ph.D. 9:05 PART 2 Enabling Backside Power Distribution Networks Sundar Ramamurthy, Ph.D. Enabling Heterogenous Chip Integration with Hybrid Bonding and Advance Substrates 9:45 PART 3 Raman Achutharaman, Ph.D. Growth in Chip Wiring and Integration 9:50 PART 4 Q&A Mehul, Sundar, Raman, Mike
2022 Master Classes APRIL MAY Sept 21 26 22* New Ways New Ways to Subscriptions to Shrink Wire and and Integrate Services Chips * Target date
T CHA IDE S Regina Freed Vice President FIRE Semiconductor Products Group
Solving the Resistance Challenges of EUV Scaling Kevin Moraes, Ph.D. Vice President Semiconductor Products Group NEW WAYS TO WIRE AND INTEGRATE CHIPS MASTER CLASS | May 26, 2022 8 Applied Materials External
Creating Amazing Digital Experiences with Billions of Transistors Chip-to-Chip On-Chip Interconnects Interconnects Brought to you by: 1. Low-resistance wiring 2. Backside power distribution networks 3. Heterogenous integration
Wiring Transistors On a Chip Interconnects Make connections laterally vertically and Lines + Vias Over 15 metal layers 4-5 layers at minimum pitch Smallest widths ~14nm Contacts Connect transistors to Via contacts interconnects Trench contacts One or two metal layers Gate Smallest widths ~12nm Fin Image source: TechInsights and Applied Materials
Creating Transistor Contacts Via contacts Top View Connect contact to Fabrication requires: interconnect Bottleneck for current flow Barrier layer to protect transistor Trench contacts Side View Seed layer to Connect contact to transistor facilitate fill Must not contaminate channel Metal fill to conduct current Contacts made of Barrier and seed layers reduce space tungsten or cobalt available for metal contact wire
Creating Interconnects Between Transistors Interconnects Fabrication requires: Lines make lateral Barrier to block connections within each Line copper diffusion layer; vias connect layers Via Liner to improve Barrier copper adhesion Chips have >50 miles of on Cu Seed layer for Line copper growth copper interconnect wiring Copper fill to com plete wire Resistance impacts power Barrier layers increase via resistance, cause and performance RC delays, waste power
Resistance Increases Exponentially as Wiring Scales Contact resistance Via resistance .) u a. ) ( . e u c a. an ( t e s c i >4x an >10x es t r s t i ac es t a r on i C V 10nm 7nm 5nm 3nm 10nm 7nm 5nm 3nm Node Node Assumptions: Dimensions scale; liner/barrier materials and dimensions do not a.u.: arbitrary units
Contact Resistance Innovations Endura® iLB PVD/ALD Endura Volta® W CVD Endura Volta Co CVD Endura Volta Selective W CVD 2010 2016 2018 2020 Radical-enhanced Tungsten carbide Cobalt fill Liner-free selective ALD TiNbarrier barrier and liner product suite tungsten fill
™ EnduraIoniq W PVD: Low-Resistance Tungsten Contacts Integrated Materials Solution™for pure tungsten metal gapfill neering, PVD Combines interface engi and CVDin high-vacuum Enablescontactscaling in a wide variety of applications
™ EnduraContact Metal IMS System Pure W fill Pure W liner Metal surface treatment Integrated Materials Solution Enables Pure Metal Contacts
Contact Resistance Innovations Continue Endura iLB PVD/ALD Endura Volta® W CVD Endura Volta Co CVD Endura Volta Endura Ioniq Selective W CVD W IMS 2010 2016 2018 2020 2022 Radical-enhanced Tungsten carbide Cobalt fill Liner-free selective PVD W liner ALD TiNbarrier barrier and liner product suite tungsten fill and CVD W fill
Innovations to Extend Copper Interconnects 2012 Endura CuBS RF XT PVD High-coverage 2014 barrier & seed Endura Volta Cobalt CVD Seed enhancing cobalt liner & selective metal cap 2018 Endura CuBS ALD/PVD 2021 ALD barrier Endura Copper Barrier Seed IMS Selective barrier & copper reflow
Copper Interconnect Fabrication Endura Copper Barrier System ECD System Integrated Materials Solution Non-integrated H* H* H* + Surface treatment PVD tantalum CVD cobalt PVD copper ECD copper fill removes residue nitride barrier liner seed
Challenges Extending Copper Interconnects at 5nm Exponential resistance increase Gapfill limitations of ECD >20nm Top Opening (a.u.) 1 sistance 2 PVD Cu seed ECD bottom-up Cu fill re <20nm Top Opening 3 ia V 10nm 7nm 5nm 3nm Node PVD Cu seed ECD bottom-up Cu fill 1 Limited space for metal wire 3 Trapped voids 2 High-resistance interfaces a.u.: arbitrary units
Lowering Via Resistance with Selective ALD Barriers Standard barrier integration Via resistance reduction Barrier .) .u Standard Barrier a e ( +100% -47% c an t s i +5% es Selective ALD barrier integration r Selective ALD barrier a i V Thin 5nm 3nm No Node dep Selective ALD removes high-resistance interface Surface Selective Treatment engineering ALD barrier
Reliable Copper Gapfillwith PVD Copper Reflow Copper reflow sequence Repeat cycles First deposition Warm reflow Wafer cool Next deposition Complete fill with PVD copper reflow Image source: Applied Materials
Unique IMS Solutions Address Resistance Issues of EUV Scaling Contact scaling with new materials / schemes .) (a.u New IMS nce solution resista Faster transistors tact Con10nm 7nm 5nm 3nm 7nm 3nm Node Interconnect scaling with new materials / schemes (a.u.) New IMS solution sistance Improved power re ia V 10nm 7nm 5nm 3nm 7nm 3nm Node
Enabling Backside Power Distribution Networks Mehul Naik, Ph.D. Managing Director and Principal Member of Technical Staff Semiconductor Products Group NEW WAYS TO WIRE AND INTEGRATE CHIPS MASTER CLASS | May 26, 2022 Applied Materials External 24
Device Scaling Approaches Contribution to Logic Density Scaling Intrinsic Scaling DTCO Intrinsic Scaling DTCO N N N+1 N+1 >50% >40% 1% >25% 16nm 10nm 7nm 5nm 3nm Source: M. Liu/TSMC, ISSCC 2021 DTCO: Design Technology Co-Optimization DTCO is becoming an increasingly important contributor to scaling
Future of Logic Scaling PPA Improvements Scaling Benefits 6 4 ↑3.5x 2 0 Performance 3.5x ↑ -2 Performance ? Area -4 Power ↓5.5x -6 ↓6.0x Power 6.0x ↓ 16/12nm 2nm -8 Planar (FinFET) 7nm 3nm (GAA) -1 0 Area 5.5x ↓ Intrinsic Intrinsic scaling scaling + 40% DTCO + >50% DTCO ? 5th Gen FinFET GAA or Variants Next Gen Planar (5nm) (2nm) Area Scaling
Limitations of Frontside Power Distribution Network Architecture Power Delivery Losses (voltage drop) Power delivery network CMOS top metal ign margin permits des 10% IR drop p Large IR drop from o r 12+ metal levels due Voltage source CMOS die e d g a t to resistance Power ol V regulator Package substrate Excessive IR drop Printed circuit board (~50%) creates reliability issues Source: Adapted from 2019 Lithography Workshop CMOS transistor
Limitations of Frontside Power Distribution Network Architecture Cell Area Scaling Challenge Gate Power rail Gate Signal line Signal line Fin Frontside power rail Removing frontside CD ~3x min CD power rail enables cell area scaling
PPACtBenefit of Backside Power Distribution Network Inflection Frontside Scheme Backside Scheme Power delivery Power and Signal lines Reduced Maintain 10% signal lines only Voltage design margin Power rail Drop Power rail Transistor Power line Area 20 to 30% Savings cell area Power delivery reduction Key changes Separation of power and signal lines Power delivery from backside of the wafer Source: Adapted from multiple IMEC and ARM publications
GAA with Backside Power Network for Additional Area Scaling 6 4 2 0 20 to 30% cell area reduction -2 Performance with Backside Power Network Area -4 Power ↓5.5x 7.5x ↓ -6 16/12nm 2nm GAA w/ -8 Planar (FinFET) 7nm 3nm (GAA) BPN -1 0 Intrinsic Intrinsic scaling scaling + 40% DTCO + >50% DTCO 20-30% area scaling from DTCO th Planar 5 Gen FinFET GAA or Variants GAA with (5nm) (2nm) Backside Power Network BPN: Backside Power Network
Backside Power Distribution Network Architecture Signal line Multiple approaches in Transistor development Power transferred to transistor using multiple approaches fs between Copper power line Trade-of power/area scaling and manufacturing complexity Power delivery from external power supply Source: Adapted from multiple IMECpublications Applied Materials External
Announced Backside Power Distribution Network Approaches Buried Power Rail Power Via Backside Contact to S/D Power Backside Buried n-TSV via power rail contact Power delivery Area Scaling Good Better Best Process Complexity Low Medium High Source: Adapted from Song et al (IEDM, 2021) Source: Adapted from public company disclosures (2021) Source: Adapted from Song et al (IEDM, 2021) with subsequent analysis by Applied Materials with subsequent analysis by Applied Materials with subsequent analysis by Applied Materials
Frontside and Backside Wafer Fabrication
Broad Portfolio Addresses all Backside Power Distribution Schemes = Broadest Portfolio of Unit Processes Co-Optimized Solutions Integrated Materials Solutions Next-Generation Scaling ™ Unit Process Leadership* Co-Optimization for IMS Metal Co-Optimized with CMP ® ® Low-Temperature Dopant Activation ReflexionLK Prime Silicon and Dielectric CMP ® ® Centura Prime Epi Endura®IMS Metal ® ® ™ Producer Eterna FCVD Silicide Backside Isolation Fill Contact Liner Fill Copper Barrier Seed VIISTA® 900 3D Implant IMS ® ® Centris SYM3 Y n-TSV Etch ReflexionLK Prime ® ® ™ New Metal CMP Olympia ALD Astra DSA Anneal n-TSV Isolation * Partial List
Frontside and Backside Wafer Fabrication Utilizing the backside of wafer for power delivery
New Ways to Integrate Chips Sundar Ramamurthy Group Vice President, GM Semiconductor Products Groups NEW WAYS TO WIRE AND PACKAGE CHIPS MASTER CLASS | May 26, 2022
Heterogeneous Chip Design –An Evolution of Moore’s Law Heterogenous integration “It may prove to be more economical to build e large systems out of smaller functions, which nu are separately packaged and interconnected.” e - Gordon Moore, 1965 v e R y r t s Flip-chip du n ERA 4: AI I r o Wire bonding t c du on c i em S ERA 3: Mobility ERA 2: PC + Internet ERA 1: Mainframe Source: SEMI, VLSI, Applied Materials https://archive.computerhistory.org/resources/access/text/2017/03/102770822-05-01-acc.pdf PC: Personal Computer AI: Artificial Intelligence
Traditional Moore's Law Scaling Hits Limits Microprocessor Trends 108 Transistor (k) 107 Single thread performance (SpecINTx 1000) 106 Frequency (MHz) Typical power (Watts) 105 Number of cores 104 103 102 101 100 1970 1975 1980 1985 1990 1995 2000 2005 2010 2015 2020 Single-threaded processor performance has plateaued despite increases in cores and transistors Application accelerator performance continues to scale with cores and transistors Source: https://www.karlrupp.net/wp-content/uploads/2018/02/42-years-processor-trend.png Source: https://www.karlrupp.net/wp-content/uploads/2018/02/42-years-processor-trend.png MHz: Megahertz Source: Yole Développement Source: https://www.techspot.com/article/2143-ryzen-5000-ipc-performance/ SpecINT: computer benchmark specification for CPU integer processing power
Transistor Counts are Hitting the Reticle Limit 1700 1500 Reticle limit 1300 2)1100 m AMD m Reticle limit (900 e iz s700 Nvidia Die 500 300 Intel Apple 100 2011 2012 2013 2014 2015 2016 2017 2018 2019 2020 2021 2022E 2023E Source: Jefferies
Opportunity: Heterogeneous SRAM Integration g n i al c ea S r A SRAM SRAM cache memory is key to performance Limited 2D scaling of SRAM impacts die size and yield Logic 28nm 16nm 10nm 7nm 5nm 3nm 2nm Source: Naffziger, VLSI Short Course, 2020 SRAM: Static Random Access Memory Source : Yole Développement
Heterogenous Integration to the Rescue GPU Memory CPU RF Image Sensor Heterogeneous integration enables logic, memory, sensors, power and communications to be combined as a system-in-package RF: Radio Frequency GPU: Graphics Processing Unit CPU: Central Processing Unit
Advanced Interconnects Enable “System-in-Package” Era Hybrid bonding Advanced substrates HBM GPU Hybrid bonding enables up to Advanced substrates connect multiple >10,000I/Os per mm2 high-performance die at high I/O density and data bandwidth HBM: High bandwidth memory I/O: Input / Output
Hybrid Bonding for High-Density Chip-to-Chip Interconnects Hybrid bonding Approaches Wafer-to-wafer Die-to-wafer Dielectric materials and copper pads fuse 2 Enables >10,000 connections per mm Requires precision in processing and alignment SoC performance can be reconstituted and Multiple hybrid bonding options expanded with hybrid bonded chiplets SoC: System on a chip
End-to-End Portfolio of Hybrid Bonding Solutions Producer® CVD Producer® Etch Endura® Mustang® Reflexion® LK ™ Integrated Materials Solution for hybrid bonding Substrate Dielectric stack Damascene RDL / Barrier / seed PVD Copper pad fill CMP with tuned Surface Hybrid bond Anneal and finish CVD pad formation etch ECD dishing control preparation (D2W or W2W) bonding Collaborating with partners to develop end-to-end technologies to ramp hybrid bonding solutions Center of Excellence investigates materials and process interactions on custom test vehicles CVD: Chemical Vapor Deposition ECD: Electrochemical deposition RDL: Redistribution layer CMP: Chemical mechanical polishing PVD: Physical vapor deposition D2W: Die to wafer W2W: Wafer to wafer
Integrated Materials Solution for Chip-to-Wafer Hybrid Bonding Film Frame Wafer Clean Wafer Clean UV: Ultraviolet
Advanced Substrates Improve I/O Density and Power 10,000 Advanced flip-chip substrates 1,000 Flip-chip substrates 2 2 m >1,000 I/O/mm m <0.1 pJ/bit r 100 e Wire bond substrates 2 I/O p 100-500 I/O/mm >1 pJ/bit 10 2 1-10 I/O/mm >10 pJ/bit 1 1000 100 10 1 Line/space pitch (µm)
System Integration with Emerging 2D and 3D Interconnects Through-Silicon Vias (TSV) Hybrid bonding Chip 1 Source: TechInsights (Chipworks) IMX260 Chip 2 Camera Module Report, 2016 Micro-bump Polymer RDL Flip-chip bump Advanced substrate Polymer RDL/ Si interposer Image Sources: SystemPlus Consulting Reports Advanced substrates package chips side-by-side with higher bandwidth (more I/Os) and lower power TSVs with micro-bumps or hybrid bonding create vertical interconnects allowing chip-on-chip stacking
Quest for Performance is Making Packages Larger Package processing must go bigger… Multiple chipletsin a package Package areas as large as 10,000mm2 Round wafers have poor area efficiency Panels enable greater number of larger packages Silicon wafer Panel
Semiconductor-Grade Large Substrate Processing ™ Applied Topaz PVD System Substrates up to 600x600mm Cluster chamber architecture Multiple applications supported Creating an industry ecosystem for semiconductor-grade panel-level packaging
Panel-Level eBeam Metrology and Test Defect review with SEM and FIB analysis Non-destructive eBeamtest Protrusion Residuals Normal interconnect Shorts highlighted Automatic defect review Fault detection by voltage contrast Precise CD measurement High-throughput analysis In-situ failure analysis Damage-free eBeam: Electron beam SEM: Scanning electron microscope FIB: Focused ion beam
Wiring & Heterogenous Integration Enable PPACt™ Scaling Low-resistance contacts and 40-50% resistance interconnects reduction @ 3nm • Lower power loss ™ • Faster switching with IMS Backside power distribution networks Up to 30% logic density • Increased logic scaling improvement • Lower power loss vs. frontside power Hybrid bonding and advanced Enables >10,000 I/Os substrates 2 per mm • Heterogenous integration and packages as large • Higher I/O and bandwidth 2 as 10,000mm • Lower power loss IMS: Integrated Materials Solution
Growth in Chip Wiring and Integration Raman Achutharaman, Ph.D. Group Vice President Semiconductor Products Group NEW WAYS TO WIRE AND INTEGRATE CHIPS MASTER CLASS | May 26, 2022 Applied Materials External 52
Semi Systems Revenue Growth Drivers Core PPACtEnablement >100% >50% $6.5B $4.8B $6.5B FY’20 FY’24* FY’20 FY’24* *Represents 2024 Financial Model High Scenario
The New Playbook ENABLED BY KEY INFLECTIONS New ASICs and accelerators New architectures New memory / in-memory compute Specialty, CIS, power GAA transistors New structures / 3D Backside power distribution 3D NAND, 3D DRAM Gate New materials Contact Interconnect EUV enablement New ways to shrink Materials-enabled patterning 3D patterning control High-bandwidth memory Advanced packaging 2.5D silicon interposer 3D TSV, hybrid bonding
Inflections Over Time LONGER TERM 3D DRAM EMERGING Forksheet CFET Gate-All-Around Backside Power EXISTING Hybrid Bonding EUV Enablement eBeam Metrology Wiring DRAM HKMG * Partial list of key inflections
Wiring Growth Opportunity Expect to grow wiring revenue at ~3X the rate of WFE 20202024 Contact Interconnect eps t S ~3X >1.5X 7nm 5nm 3nm 7nm 5nm 3nm Applied’s wiring opportunity increases by >$1B from 7nm3nm *Leading Foundry/Logic Customers
Positioned for Growth in Packaging Early innings of multi-year growth #1 in bond pad, bump and TSV Broad product portfolio + full-flow lab ~$500M Key ecosystem partnerships Delivering system level PPACt gains: ↓ R, ↓ power, ↓ area, FY’20 FY’24F ↑ performance
Packaging Growth Opportunity Revenue Growth Revenue Goal >50% YoY >10% CAGR FY’15 FY’20 FY’21 FY’20 FY’23 FY’24
Packaging Portfolio PVD Plating CMP CVD Etch Future Integrated Materials Solution for hybrid bonding Large-area metrology and Endura® Mustang® Reflexion® LK Producer® CVD Producer® Etch process control
Broad Portfolio Addresses all Backside Power Distribution Schemes = Broadest Portfolio of Unit Processes Cooptimized Solutions Integrated Materials Solutions Next-Generation Scaling Buried Power Rail Power Via Backside Contact to S/D Backside Power Delivery Approaches Logic Density, Low Medium High Process Complexity
Inflections Over Time LONGER TERM 3D DRAM EMERGING Forksheet CFET Gate-All-Around Backside Power EXISTING Hybrid Bonding EUV Enablement eBeam Metrology Wiring DRAM HKMG * Partial list of key inflections
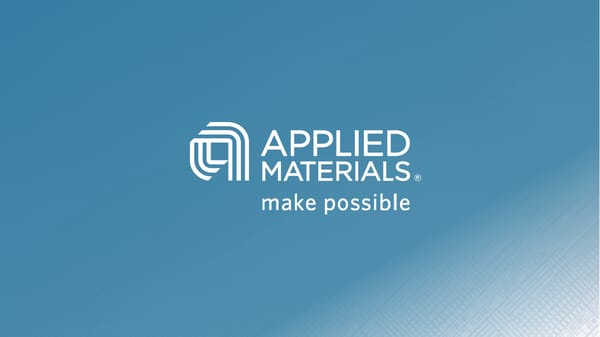